The customer currently outsources the process to braze brass fittings into the brass housing. The cost of this outside processing is $30 per part. By in-sourcing, the part cost will be reduced, and the customer can also avoid delays in the outsourcing process.
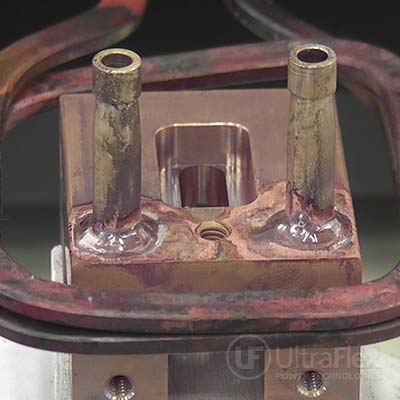
Equipment
Materials
• Silver brazing preform.
• Stay-Silv brazing flux
• Silver brazing preform.
• Stay-Silv brazing flux
Key Parameters
Temperature: approximately 677°C
Power: 1.98 kW
Time: 150 seconds
Temperature: approximately 677°C
Power: 1.98 kW
Time: 150 seconds
Frequency
71 kHz
71 kHz
Process:
- Braze Brass Fittings into Brass Housing: the barb fittings are positioned into the housing, with a pre-form placed at the position of the joint.
- The assembly is then positioned into the induction coil.
- At approximately 2:15, a small amount of brazing alloy is added by hand during the heating, to fill the opening not covered by the preform. A production preform would completely encircle the part, and not have a gap.
- The finished braze, shows a consistent fillet at the braze joint.
Results/Benefits:
Enables in-sourcing of an assembly process that has been done by a supplier. Avoids costly delays in processing.
- Precise control of the time and temperature
- Power on demand with rapid heat cycles
- Repeatable process, not operator dependent
- Safe heating with no open flames
- Energy efficient heating
Pictures
![]() |
After approximately 30 seconds. |
![]() |
After approximately 1 minute. |
![]() |
After approximately 90 seconds. |
![]() |
After approximately 2 minutes. We see a small gap not covered by the preform. |
![]() |
After approximately 2:15. A small amount of brazing alloy is added by hand during the heating, to fill the small gap not covered by the preform. |
![]() |
The finished braze after 2:30, shows a consistent fillet at the braze joint. |
Videos
CONTACT!
Do you have a heating application? Contact Ultraflex Power Technologies. Ultraflex can provide a custom induction heating solution to meet your application and manufacturing requirements.